在当前的半导体制造体系中,物联网与自动化设备的深度融合正重塑物料流转逻辑——曾经的"人找料"模式,已升级为依托实时数据交互的"料等人"智慧体系,高强度、低灵活性的传统物料运输被精准高效的智能调度取代,完成了半导体制造从"被动响应"到"主动预判"的跃升。
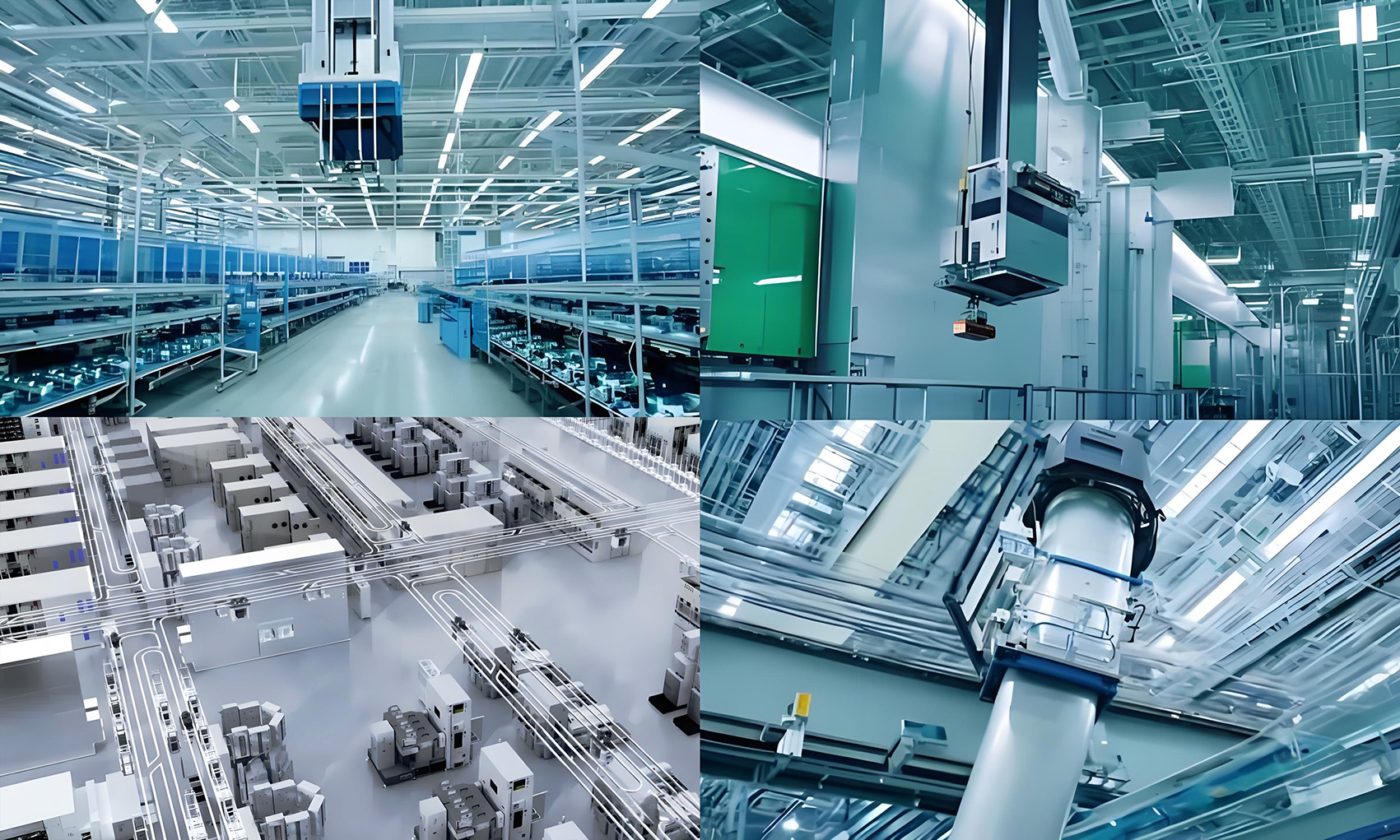
一套完整的天车系统(含轨道、吊具、控制系统)造价高达500-800万元,大型晶圆厂需部署多套系统,设备采购成本占比高。
天车轨道需定期校准(年均费用约30万元/公里),吊具机械部件易损耗,单台天车年运维成本普遍超50万元。
为保证生产供应,企业常需配置多台天车"备用待命",但产线需求波动时,闲置天车的电能损耗仍占总能耗的20%-25%。
不可忽视的是,随着半导体制造的"多品种、小批量"转型,天车的"刚性运输"与半导体物料的"柔性需求"矛盾凸显:当产线临时调整排程,天车需重新规划路径,空驶调整时间占比达15%,进一步推高了综合成本。
上海科浩RFID通过在储位嵌入的读写模块,可自动识别载具上的RFID标签,实现"物料—货架"的无感交互:
-
入库即建档:
上架时,货架自动读取标签内的物料ID,并同步至MES系统,同时也可以从MES系统获取该物料的生产信息,整个过程无需人工扫码或手动录入。
-
实时定位:
系统精准记录物料在货架上的位置,电子货架系统图实时显示物料位置信息,实现一秒快速找货的需求。
AGV小车与RFID货架深度联动,形成"需求触发—路径规划—精准运输"的智能链路:
-
按需召唤:
产线需要某片光罩盒时,调度系统自动发送指令,AGV前往目标货架,取料后直接送达工位,全程无需人工干预。
-
动态调度:
实时监测产线需求波动,自动调整AGV任务。即使多工序同时需求物料,也能通过快速分配运力,避免产线停滞。
-
成本优化:
AGV小车无需轨道铺设、无需频繁维护,企业可根据产线需求灵活增减,降低投入与闲置成本。
上海科浩RFID货架+AGV小车+MES系统的数据互联互通,构建起"物流—生产"的数字孪生平台:
-
成本可视化:
可实时查看单位运输能耗、设备利用率等核心指标,清晰掌握成本。
-
效率最优化:
通过历史数据,分析高峰时段物料需求,调配AGV数量,避免"忙时不够用、闲时全闲置"。
-
风险可追溯:
假若某批次产品良率异常,可快速调取对应运输记录,精准定位是否因运输环导致损伤,缩短客诉处理周期。
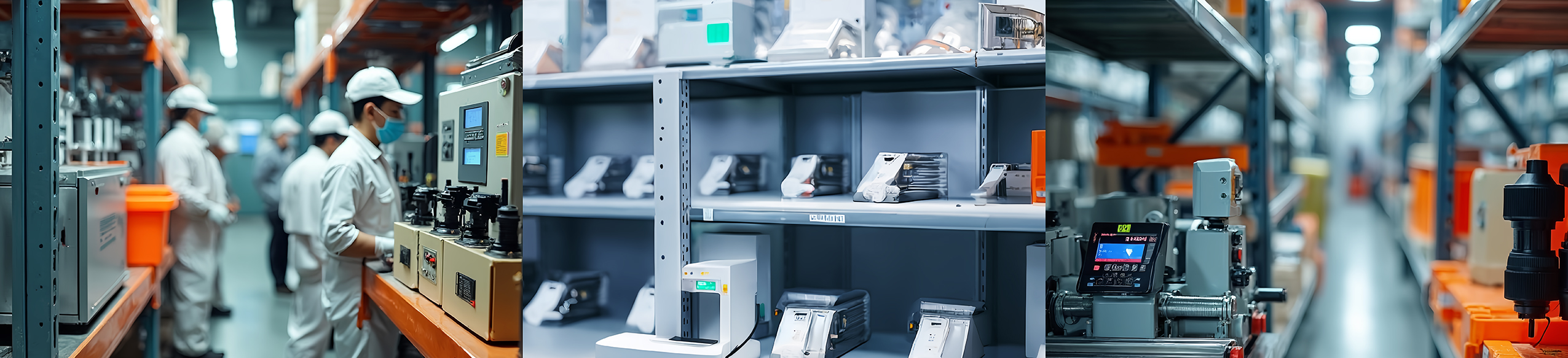
上海科浩RFID货架已在江苏、湖北、福建、安徽等多地晶圆、芯片、封装企业获得成功应用,实际数据验证了经济性与可靠性。以江苏某晶圆厂为例:
从“需求提出”到“送达工位”,平均耗时大幅缩短。
设备投入显著降低,年运维成本、综合物流成本也显著下降。
数据与库存偏差率降低,临时调用响应时间显著缩短。
物料存储环境异常率得到改善,报废率显著下降。
"现在找料,一看系统就能准备定位,大大节省了找料时间。"物料员的感慨,也印证了RFID货架对"找料效率"的提升。
依托自主研发的多元化产品矩阵(RFID解决方案、智能CIM系统、高精度视觉产品、全场景自动化产品),上海科浩为企业提供从单点到全链的技术支撑,通过持续迭代的服务生态,助推"数据与技术"驱动的能效革命。
专注制造业信息化 / 提供系统解决方案
上海科浩信息科技有限公司秉承"勇于创新,追求卓越"的经营理念,以“服务制造,协同共赢"为宗旨,形成了以CIM产品线、视觉产品线、工业自动化产品线为主的业务体系,致力于成为中国领先的制造业信息化、自动化、智能化整体解决方案提供商。
凭借深厚的技术积累和丰富的项目实施经验,公司主导落地了多个大型自动化软件系统的方案及实施。
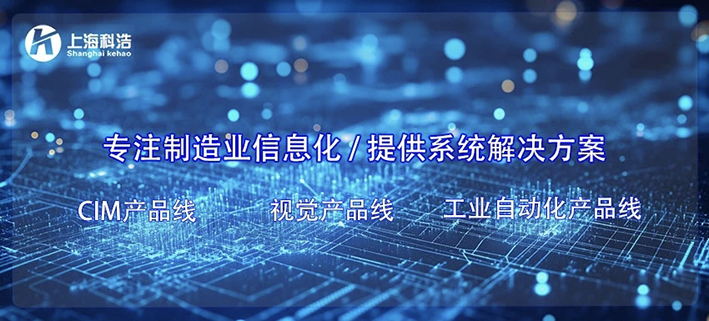